A New Path in 3D Printing: Lightweight Automotive Parts Without Compromise
In the quiet halls of Tohoku University’s Institute for Materials Research, a team of scientists has made a significant leap forward in the field of additive manufacturing. Their breakthrough promises to redefine how automotive components are designed, using a cutting-edge multi-material 3D printing process to create a lightweight yet durable suspension tower.
The innovation hinges on solving a long-standing challenge in the world of metal 3D printing, where precision meets complexity. This technique involves layering metal powders and fusing them with heat to create intricate, highly customizable shapes. For the automotive industry, it offers the dream of parts that are lighter, stronger, and more resource-efficient. Yet, for all its promise, the method comes with a significant obstacle: combining materials like steel and aluminum often leads to brittle connections that weaken the final product.
The Promise and Pitfalls of Multi-Material 3D Printing
“Multi-materials are a hot topic in additive manufacturing,” explains Associate Professor Kenta Yamanaka from Tohoku University. By strategically combining metals, manufacturers can craft parts that balance strength and weight—qualities vital for everything from suspension towers to aerospace components. For example, blending durable steel with lightweight aluminum can significantly reduce a car’s overall weight, improving fuel efficiency or extending the range of electric vehicles.
But this combination isn’t straightforward. When steel and aluminum meet, they form brittle intermetallic compounds—chemical structures that are far from ideal for demanding applications. Instead of achieving the sought-after balance between lightness and durability, the materials risk becoming fragile and prone to failure.
A Laser-Focused Solution
To overcome this, Yamanaka’s team turned to Laser Powder Bed Fusion (L-PBF), one of the most advanced metal 3D printing techniques. This technology uses a laser to precisely melt metal powders, layer by layer. But precision alone wasn’t enough. The researchers realized they needed to tweak the process itself.
By increasing the laser’s scan speed, they discovered they could suppress the formation of brittle intermetallic compounds like Al5Fe2 and Al13Fe4. This faster scanning resulted in a phenomenon known as non-equilibrium solidification, a process where the metals cool and solidify so quickly that weak points in the material structure are minimized.
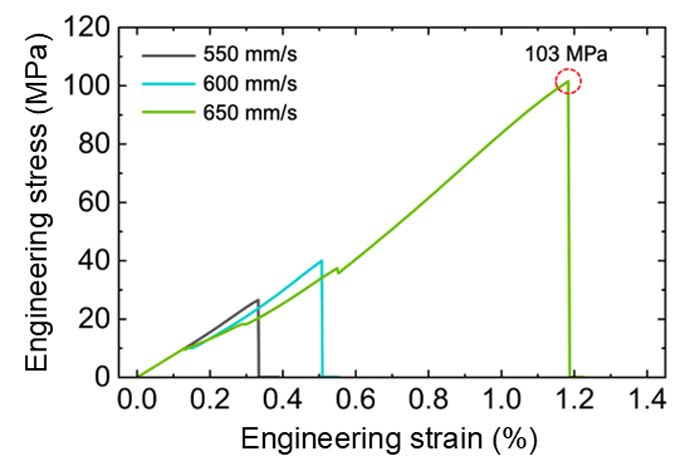
“In other words, you can’t just slap two metals together and expect them to stick without a plan,” explains Specially Appointed Assistant Professor Seungkyun Yim. “We had to fully understand the in-situ alloying mechanism first.”
A World-First Automotive Component
Armed with their refined process, the team achieved what was previously thought impossible: the world’s first full-scale multi-material automotive suspension tower, designed with a tailored geometry. The result was not only lightweight but also exceptionally durable, demonstrating the potential of their breakthrough for other demanding applications.
This innovation is more than a single success—it opens doors for multi-material combinations beyond steel and aluminum, paving the way for advancements in aerospace, construction, and renewable energy systems.
Building the Future
As industries push for lighter, stronger, and more sustainable materials, Tohoku University’s research offers a glimpse of what’s possible. By mastering the delicate interplay between dissimilar metals, they have laid the foundation for a new generation of 3D-printed components that don’t compromise on strength or reliability.
Their journey underscores the importance of understanding not just the materials themselves, but the science of how they bond and perform together. It’s a reminder that innovation often lies in the details, and for Tohoku University, those details are shaping the future of manufacturing.
Original Story: Research News – How to Print a Car: High-performance Multi-material 3D Printing Techniques | Tohoku University Global Site