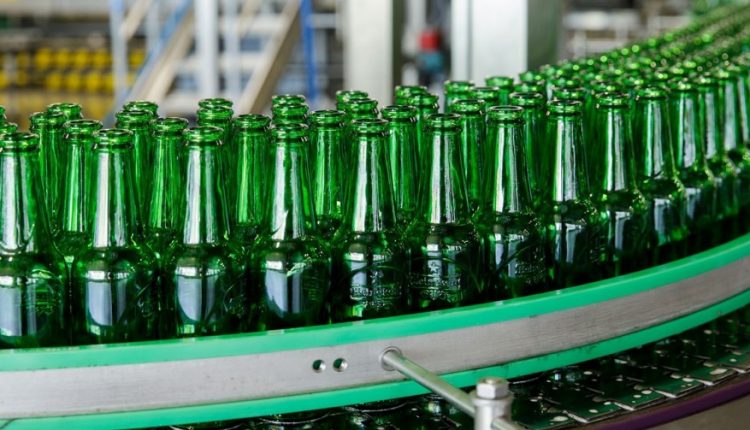
How 3D Printing is Shaking Up the Manufacturing Industry
3D Printing isn’t a new technology. It’s been in action since the late 1990’s. But over the last decade, this technology has successfully strengthened its presence in the manufacturing industry. With both consumer and commercial grade 3D printers on the market, the manufacturing industry is visualizing (and bringing to life) an entirely new mode of production. As 3D printing has gotten more versatile and extremely affordable, more and more companies have taken advantage of it, on a path to change the way our world is produced.
Just recently, Heineken announced that it was streamlining the manufacturing processes at its 150 breweries by establishing a 3D printing lab where it aimed to maximize output, up-time, and safety in its factories. The company began by 3D printing improved safety latches that were used during machine maintenance. It followed with spare parts production and expanded to other tools that made production more efficient. Other companies such as GE work to implement 3D printing even more effectively into the aerospace industry for weight reduction and use of fewer parts. Back in 2019, the company produced LEAP-1A engines that included 19 3D printed nozzles. The industry has embraced the engines along with the incorporation of 3D-printed parts.
The Benefits of 3D Printing in Manufacturing
3D printing plays multiple roles in the manufacturing process, and it is poised to roll out even more benefits, as it is advanced and refined
Currently, designing and prototyping are two of the major processes that stand to gain the most from 3D printing tech. This technology is also useful for low-volume production, especially when small amounts of product are needed for testing the market or advertising at shows. With time, the production capabilities of 3D printers will continue to scale.
The most meaningful and impactful benefit to the manufacturing industry that this technology brings with it is its ability to reduce both the time and cost for achieving a viable product. Perhaps this is the reason more industry insiders are encouraging the process and willing to adapt. Several companies are now looking to exploit this technology in order to see greater profits. This will include innovations that have a much greater impact than mere replacements in the manufacturing industry.
Scopes of Customization
3D printing allows manufacturer to make multiple designs with a single machine. Many businesses roll out custom-built products by combining 3D printing with 3D scanning technology. For instance, 3D printing is used for creating prosthetic limbs that are not just economical but are also accurate. Other companies offer custom options for multiple products such as earbuds that can be further fitted in a users’ ear or shoes that perfectly conform to the size of a wearers’ feet.
Advanced Designs
As 3D printers become more flexible, design teams have an opportunity to tweak the structures that seem strong or interesting. This, in turn, allows them to craft complex, geometric shapes that couldn’t be realized by the previous methods. With newer design goals, these businesses intend to encourage customers to think differently. Most industries are using this technology to create lightweight, lattice like structures for reducing the material used. They are also combining assemblies to cut down on labor costs and reduce potential failures.
More Prototypes
3D printers have also drastically reduced the time needed to create new prototypes. Cheaper and quicker production of prototype speeds the process of product development which reduces multiple costs across the board. 3D printing is being extensively used for prototyping new products in order to provide designers with a chance to explore multiple options. Previously, most of the designs were manufactured in the analog processes like injection molding.
Availability of Replacement Parts
As 3D printing becomes more prevalent in the manufacturing industry, more machines are being designed with the 3D-printed parts. The benefit of this process is the fact that a printed part can be easily replaced with a 3D printed part. Industrial equipment, for instance, can even be easily shipped with digital blueprints of various parts allowing the end-user to create the replacement part. Ultimately, this process reduces dreaded and costly factory downtime.
Low-Volume Production
3D printers also make low-volume production easier. Focused product teams can roll out new products at faster speeds with fewer capital constraints, ability to improve products quickly and then create accelerated versions of their old counterparts.