How plastic LCDs are shaping new designs
Flexible displays have been around for a number of years in different forms, but we are only at the beginning of discovering how flexible displays can transform product design, and bring about new use cases, as Paul Cain, Strategy Director at FlexEnable explains.
So far we have seen smartwatches that use flat, plastic OLED displays, allowing the watch to be thinner (or have a bigger battery for the same thickness); edge-to-edge displays in Samsung smartphones that are planar across most of the phone’s surface, but curved along two parallel edges; and non-rectangular notched displays in the next iPhone X. Each of these three examples is exploiting a different attribute of plastic active-matrix displays, and yet there is so much more that will be possible in the next few years. Undoubtedly, flexible plastic displays have the potential to transform many applications across different industries including automotive, consumer electronics, smart home appliances and digital signage, and bring surfaces to life.
Flexible display technologies
There are several types of flexible display either in mass production or coming soon. Flexible OLED displays are perhaps the most commonly discussed and commercialised. They offer excellent colour gamut and industry leading contrast, and are already used in smartwatches and mobile phones. Today nearly all supply comes from Samsung Display, but many other display makers are investing into OLED capacity, particularly in China.
However, the cost of manufacturing these displays is still very high, due to both higher materials cost and lower yield in the production process compared with LCDs. This is in part related to how the plastic display is removed from the carrier glass on which it is mounted during display manufacture. For this and other manufacturing reasons it is therefore difficult to cost effectively scale flexible OLED displays to large sizes today.
From a performance perspective, one of the challenges with flexible OLED displays is lifetime – which today is suitable for mobile devices, but still needs further improvement to meet the needs of applications such as automotive, where the display must be both high brightness and have a long lifetime. Automotive displays today are therefore nearly all LCD.
From a reliability point of view, LCD has better performance – partly because LCD is easier to drive than OLED, but also because increasing the LCD display brightness does not reduce its lifetime, because light is produced independently by the backlight unit.
OTFT enabled plastic LCDs
FlexEnable has developed a flexible organic LCD (OLCD) that is four times thinner (less than 0.3mm) and more than ten times lighter than conventional glass-based displays. With a bend radius that can go up to 10mm, OLCD can be conformed, shaped and wrapped around surfaces.
OLCD uses organic transistors, which have better electrical performance (mobility) than the amorphous silicon thin-film transistors (TFTs) that they replace. These organic TFTs (OTFTs) are manufactured using a solution processing approach, where the organic polymer semiconductors and dielectrics are deposited at low temperatures – below 100°C.
The low manufacturing temperature means that low cost plastic substrates can be used, such as TAC film. TAC is a material commonly used to manufacture polariser sheets in today’s glass LCD displays – because it has excellent optical properties (optical transmission of around 94%), and it lets light pass through it without affecting its polarisation (‘very low birefringence’) – meaning that OLCDs made with it can have contrast every bit as good as the glass LCD displays of today, but with the benefits of plastic.
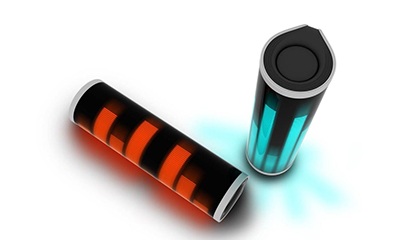
OTFTs don’t just bring manufacturing and mechanical benefits to displays, but also electrical. Compared to today’s silicon TFTs, OTFT has incredibly low leakage current – almost 1,000 times lower than in amorphous silicon (a:Si) TFTs. This has important power saving benefits for displays, particularly for applications where stable images need to be displayed for long periods, such as digital signage and automotive.
One of the strikingly different attributes of OLCD compared to other flexible display approaches is its natural scalability to large sizes, for two reasons. Firstly, the LCD frontplane is optically just like a conventional LCD, except that it is made on plastic instead of glass; LCD has been manufactured for very large displays (>80”) for many years making it the most common and trusted display technology today. Secondly, because the backplane (TAC) is processed at low temperatures, a simple handling method is possible – that means the TAC can be mounted to, and then released from, are-usable carrier glass with ~100% yield regardless of size.
Plastic OLCDs can also be easily cut to non-rectangular shapes by laser profiling offering a greater degree of design freedom. Once the display has been built, the plastic substrate can be gently released from the rigid carrier ensuring a simple, reliable high yield ‘release’ process.
OLCD therefore offers for the first time large area, high brightness flexible displays with long lifetime – as needed to serve a range of applications described above that cannot be easily satisfied with other approaches to flexible display.
Scaling OLCD to production
FlexEnable recently announced a technology transfer and licensing deal with Chinese display maker Truly Semiconductors, to bring conformable plastic OLCDs into mass production by the end of 2018. FlexEnable’s OLCD manufacturing process has been deliberately designed to be implemented into existing a:Si TFT LCD manufacturing lines. The ability to put the process into existing lines, using existing equipment, means capacity can be brought online more quickly and cost efficiently. This, combined with the large area scalability and electrical performance of OTFT, opens the door to serve pent-up demand in a range of applications across automotive, consumer electronics, digital signage and beyond.
Unlocking design freedom
We are so used to thinking of displays as flat glass surfaces that we forget how much this constrains where and how we use them in our lives. Design engineers want to be able to seamlessly integrate displays into products regardless of the product form factor. Flexible displays are also needed to enable new use cases in applications where previously there has been no display due to the design limitations of glass displays.
For example, plastic, conformable and shapeable displays will be a perfect solution to design challenges associated with consumer electronics as they allow the integration of displays into existing product designs without having to redefine (or flatten) the surface of the object, providing a more natural and subtle way of bringing interactive surfaces into our homes.
The automotive industry is another sector where large area flexible displays will be a game-changer. In today’s car interiors, the display is almost the only remaining flat surface, representing a major design constraint. With a growing trend for large area in-vehicle displays, there are many new applications that displays can address as they become thin, light, shatterproof and conformable to any surface. For example, a curved display on the A-pillar of the car can replace the wing mirror (for increased aero dynamic efficiency) or show the driver what is behind the pillar. A plastic display that conforms to the interior surfaces of the car can enable a full display dashboard that provides infotainment to the users.
Digital point of sale (PoS) displays with unconventional shapes are also needed in the retail sector where they are used for distributing content and advertising. The ability to wrap those displays around surfaces can transform the shopping experience.
Flexible displays will change the rules of where and how displays are integrated and used in products – where a ‘product’ in this context could be anything from tablets to tables. We will soon start to see use cases for displays that could not even have been considered with flat glass displays. Eventually all displays will be manufactured on plastic, and we will look back on glass displays with the same nostalgia currently reserved for Cathode Ray Tubes.