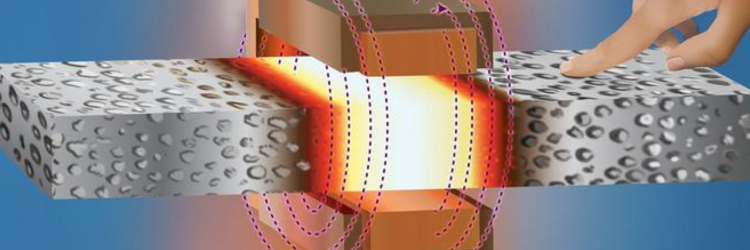
Weld Metal Foam Without Melting its Bubbles
North Carolina State University researchers have identified a welding technique to join composite metal foam (CMF) components without impairing the properties that make CMF desirable. CMFs are ideal for a wide array of applications because their air pockets make them light, strong, and effective at insulating against high temperatures. Their paper, “A Study on Welding of Porous Metals and Metallic Foams,” was published in the journal Advanced Engineering Materials.
CMFs consist of hollow, metallic spheres from materials such as stainless steel or titanium embedded in a metallic matrix made of steel, titanium, aluminum, or other metallic alloys.
The material is lightweight and remarkably strong, with potential applications ranging from aircraft wings to vehicle armor and body armor.
CMF is also better at insulating against high heat. The combination of weight, strength, and thermal insulation means that CMF could be used in storing and transporting nuclear or hazardous materials, explosives, and other heat-sensitive materials. However, manufacturers would need to weld multiple CMF components together. This has posed a problem.
Traditional fusion welding uses a filler to connect two pieces of metal, which is problematic because the melted metal fusing the two pieces of CMF is solid, lacking the desirable properties of the CMF on either side. Welding that uses direct heat to melt the metal results in some of the porosity in the CMF being filled in, impairing its properties.
The researchers identified a form of welding called induction welding, which uses an induction coil to create an electromagnetic field that heats the metal for welding. The electromagnetic field can penetrate deeply into the material, allowing for a good weld. The air pockets that make up the remaining 65-70% of the CMF insulate the material against
the heat, allowing induction welding to heat up the targeted area for joining two pieces of CMF, yet preventing the heat from spreading out from the join site, which helps to preserve the CMF’s properties.